By using electric and hybrid forms of propulsion, very different-looking aircraft may end up taking to the sky
Sep 18th 2015 | From the Economist
WHEN Didier Esteyne, an Airbus test pilot, flew a small two-seat electrically powered aircraft called the E-Fan across the English Channel in July, the giant European aerospace group was keen to point out the journey was not a gimmick. Indeed, Airbus is serious enough about electric flight to want to put the E-Fan into production as a pilot-training aircraft. It will go on sale towards the end of 2017 to be followed by a four-seat version.
Airbus is not alone in thinking about making much bigger electric and hybrid aircraft to carry passengers. Just as in cars, electrical propulsion offers a number of advantages over piston and jet engines. Modern, digitally controlled electric motors supply lots of torque, a rotational force which is as good at turning propellers and fan blades as it is wheels. Electric power is also quiet, clean and highly reliable, with fewer engine parts to wear or break.
Batteries, it is true, do not provide the range many would like: lithium-ion ones allow the E-Fan to fly for about an hour with a 30-minute reserve. That may be fine for a flying lesson, but not for a passenger airliner. Batteries, though, are steadily improving and, because aircraft have long service lives (the Boeing 747 first flew in 1969), aerospace engineers work on projects set well into the future.
What really excites them about electric propulsion is that it provides the opportunity to build radically different aircraft, like the Airbus E-Thrust concept illustrated above. The idea is that instead of hanging big and heavy jet engines below the wing, a greater number of small and lighter electrically driven fans or propellers could instead be incorporated into other areas of an aircraft. Doing this with lots of small conventional engines would be complicated and would add a lot of weight. But electric motors make the concept, called distributed electric propulsion (DEP), feasible. The advantage of distributing power is that it can be used to increase the airflow over the wings and thus allow an aircraft to fly more efficiently. “DEP enables a fundamental shift in how we design aircraft,” says Mark Moore, a principal investigator into electric flight at NASA’s Langley Research Centre in Virginia.
On the runway
NASA spins the props
NASA is testing a DEP wing mounted above a truck and driven at high speed across a dry lake bed at Edwards Air Force Base in California. The wing uses 18 small, electric propellers strung along its leading edge. The next step is a project called Sceptor, which involves replacing the wing on a conventional four-seater light aircraft—in this case, a twin-engined Italian-built Tecnam P2006T—with a DEP wing containing a dozen or so electrically driven propellers (see photo). Sceptor is due to begin test flights in 2017.
Sceptor’s line of small propellers will increase the aircraft’s lift at lower speeds, allowing it to take off and land on shorter runways. It also means the wing could be made more slender, perhaps only a third of the width of the wing on a conventional aircraft, thus saving weight and fuel costs. Typically the wing on a light aircraft is relatively large to prevent it from stalling (which happens at low airspeeds, when the wing cannot provide sufficient lift). But large wings are not very efficient when an aircraft is cruising because they create a lot of drag. Sceptor’s wing will be optimised for cruise, yet still provide enough lift to help prevent stalling on take-off or landing.
The wing will also be capable of other tricks. The speed of each electric propeller can be controlled independently, which provides the ability to change the pattern of airflow over the wing to cope with rapidly changing flying conditions, such as wind gusts. When cruising, the propellers closer to the fuselage could be folded back, leaving those on the wing tips to do the work. If Sceptor’s test flights are a success, the technology could be incorporated into small commuter aircraft within a decade, even with present progress in battery development. These aircraft, says Mr Moore, would have no in-flight emissions, be extremely quiet and reduce operating costs by around 30%.
Airbus’s E-Thrust concept is further from the runway. A collaborative project with Rolls-Royce, a British manufacturer of jet engines, and other research groups, the aircraft, or something like it, is projected to enter service around 2050. By then, the European Union expects the aviation industry to have cut fuel consumption, emissions and noise from passenger aircraft by at least 20-30%, relative to today’s state-of-the-art designs.
The goal of the E-Thrust is to meet such targets and be able to carry around 90 passengers on flights of two hours or more, and still have a generous safety margin from its batteries. This, though, will require a breakthrough in the technology to store electricity—which might well happen over the next few decades. The concept also uses distributed propulsion, but with a twist because it is hybrid.
A traditional jet engine sits in the tail of the E-Thrust. It also has three electrically driven fans on each wing. On take-off, the jet and all six electric fans will be used to provide maximum lift. When the aircraft reaches its cruise altitude, the jet can be throttled back but is powerful enough both to power the fans and to top up the batteries. During descent, both the jet and the fans will be turned off. As the aircraft glides, the oncoming air will turn the fans so that they work like wind turbines to top up the battery some more. The fans will be used to land, with the jet ticking over ready to provide additional thrust should the aircraft need to go around again.
One advantage of the hybrid system is that it provides a massive boost to a jet aircraft’s “bypass” ratio. This is a measure of the amount of air that flows around the hot core of a jet engine compared with that which goes through it to provide oxygen in the combustion chamber. The jet engines on early passenger aircraft had a low bypass ratio, producing a lot of their thrust from the fast-moving air blasting out of the rear of the core. This made them noisy and fuel-hungry. As the blast leaves the core it turns a turbine, which via a shaft turns a fan at the front of the engine to draw in more air. By making the fan larger, it has been possible to move a bigger volume of slower-moving air (the bypass) around the outside of the core. This is more efficient and much quieter. It is also the reason why jet engines have over the years got fatter.
Modern jets have a bypass ratio of up to 12:1 compared with about 5:1 or less in the 1970s. But making the fans even larger is becoming difficult as they take up more and more room under the wing. And bigger engines need stronger wings, which adds to an aircraft’s weight. The hybrid set up in the E-Thrust neatly gets around these problems because only the jet engine in the tail has a fuel-burning core. This means all of the air flowing through the six electrically driven fans contribute to its “effective” bypass ratio of 20:1 or more. This would make the aircraft extremely fuel-efficient and very quiet.
Smooth operator
Another efficiency comes from the distributed engines “ingesting” what is called the boundary layer of air flowing over the wing. This is a very thin layer of air close to the surface of the wing. It is slowed down by friction as molecules of air touch the wing’s surface. The boundary layer passing over the raised upper surface of the aerofoil shape of a wing (which provides a wing with its lift) can become turbulent, which helps produce the wake which a jet aircraft leaves behind. By positioning the E-Thrust’s electric fans above the wing to intercept the boundary-layer air, the fans can accelerate it, which reduces drag from the wake.
Technical advances in two areas are needed for the E-Thrust to fly. Besides better batteries the other is superconductivity, a phenomenon that removes electrical resistance when certain materials are cooled below a critical temperature. Reducing resistance allows construction of electrical and motor systems light and powerful enough to fly the aircraft. This has been done on a small scale, in equipment such as hospital scanners. But for an aircraft it will require intense cooling at a level beyond anything commercially available. A group at the University of Cambridge is working with Airbus on that problem.
Get over those hurdles, and electric aircraft will gather momentum. They will start off small but get bigger and carry more passengers as technologies improve. Some of those technologies, Airbus expects, will also help make traditional jet aircraft more efficient and quieter, too.
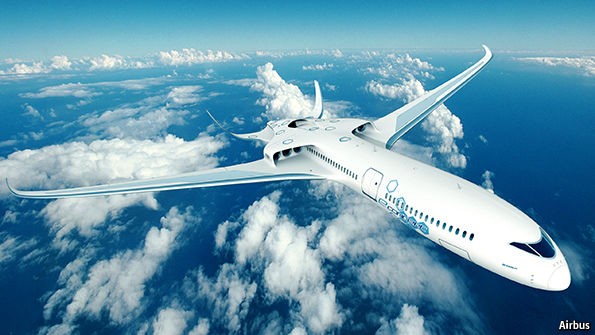