From The Economist
Bioprinting: Building living tissue with a 3D printer is becoming a new business, but making whole organs for transplant remains elusive
Mar 8th 2014
IN A state-of-the-art clean room, a scientist clad in a full-body containment suit, a hair net and blue gloves is preparing some printing cartridges—filled not with ink but a viscous milky liquid. Next to her sits a computer connected to a machine that resembles a large ice-cream dispenser, except that each of its two nozzles is made of a syringe with a long needle. Once the scientist clicks on the “run program” button, the needles extrude not a vanilla or chocolate-flavoured treat, but a paste of living cells. These bioinks are deposited in precise layers on top of each other and interspersed with a gel that forms a temporary mould around the cells.
Forty minutes later, the task is finished. Depending on the choice of bioink and printing pattern, the result could have been any number of three-dimensional biological structures. In this case, it is a strand of living lung tissue about 4cm in length and containing about 50m cells.
Since its inception in 2007, researchers at San Diego-based Organovo have experimented with printing a wide variety of tissues, including bits of lung, kidney and heart muscle. Now the world’s first publicly traded 3D bioprinting company is gearing up for production. In January samples of its first product—slivers of human liver tissue—were delivered to an outside laboratory for testing. These are printed in sets of 24 and take about 30 minutes to produce, says Keith Murphy, the firm’s chief executive. Later this year Organovo aims to begin commercial sales.
Each set consists of a plate with 24 wells containing a piece of liver tissue 3mm square and 0.5mm deep. Although prices have not been fixed, a set of tissues like this can sell for $2,000 or more for laboratory use. It might seem expensive, but it could save pharmaceutical companies a lot of money. This is because Organovo’s research indicates that the slivers of liver respond to drugs in many ways like a fully grown human liver would. If this is confirmed by outside testing, researchers could use the printed tissues to test the toxicity of new drugs before deciding whether to embark on expensive clinical trials with patients.
The invention of 3D printing in the 1980s provided a technology now used to manufacture everything from aircraft parts to prosthetic limbs. But the promise of 3D bioprinting is even larger: to create human tissues—layer by layer—for research, drug development and testing, and ultimately as replacement organs, such as a kidney or pancreas, for patients desperately in need of a transplant. Bioprinted organs could be made from patients’ own cells and thus would not be rejected by their immune systems. They could also be manufactured on demand.
At present only a handful of companies are trying to commercialise the production of bioprinted tissues. But Thomas Boland, an early pioneer in the field, says that plenty of others are interested and estimates that about 80 teams at research institutions around the world are now trying to print small pieces of tissues as varied as skin, cartilage, blood vessels, liver, lung and heart. “It’s a wonderful technology to build three-dimensional biological structures,” says Gabor Forgacs, who co-founded Organovo in 2007 and was the company’s scientific mastermind.
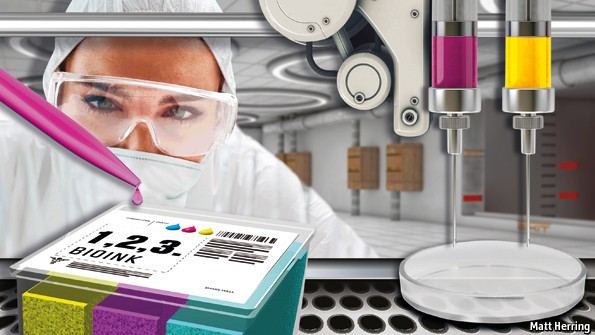